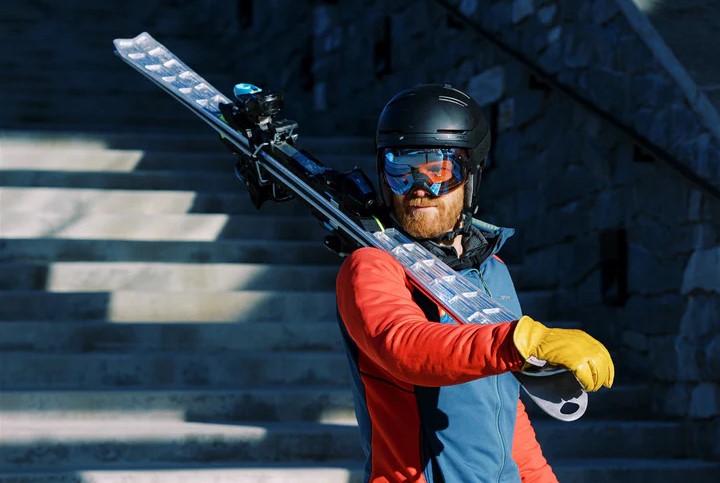
Ski design has undergone a remarkable evolution, from early hickory planks to the advanced composite technologies of today. The latest innovation, however, comes in the form of skis milled entirely from aerospace-grade aluminum. This shift, spearheaded by Metal1 Skis Corporation (M1 Skis), represents a radical departure from traditional ski construction and a leap forward in performance, durability, and sustainability.
The idea of aluminum skis traces its origins to Brian Rosenberger, an aircraft manufacturing expert who envisioned a ski shaped entirely from a solid aluminum block. Using his aerospace background, Rosenberger, with financial backing from Ron Chambers and input from Leif Sunde of Denver Sports Lab, developed and refined aluminum ski prototypes over the years. In 2023, their efforts culminated in the launch of M1 Skis, with a mission to redefine skiing technology.
Why Aluminum?
Aluminum offers a unique combination of strength, flexibility, and resilience. Unlike conventional skis with cores susceptible to water damage and delamination, aluminum skis are impervious to moisture, eliminating core shots (because there is no core), and edge rusting. The aluminum base is hard yet ductile, resists chipping, and absorbs impacts better than polyethylene bases. The skis maintain edge sharpness, glide, and tuning integrity over extended periods, thanks to the durability of their material.
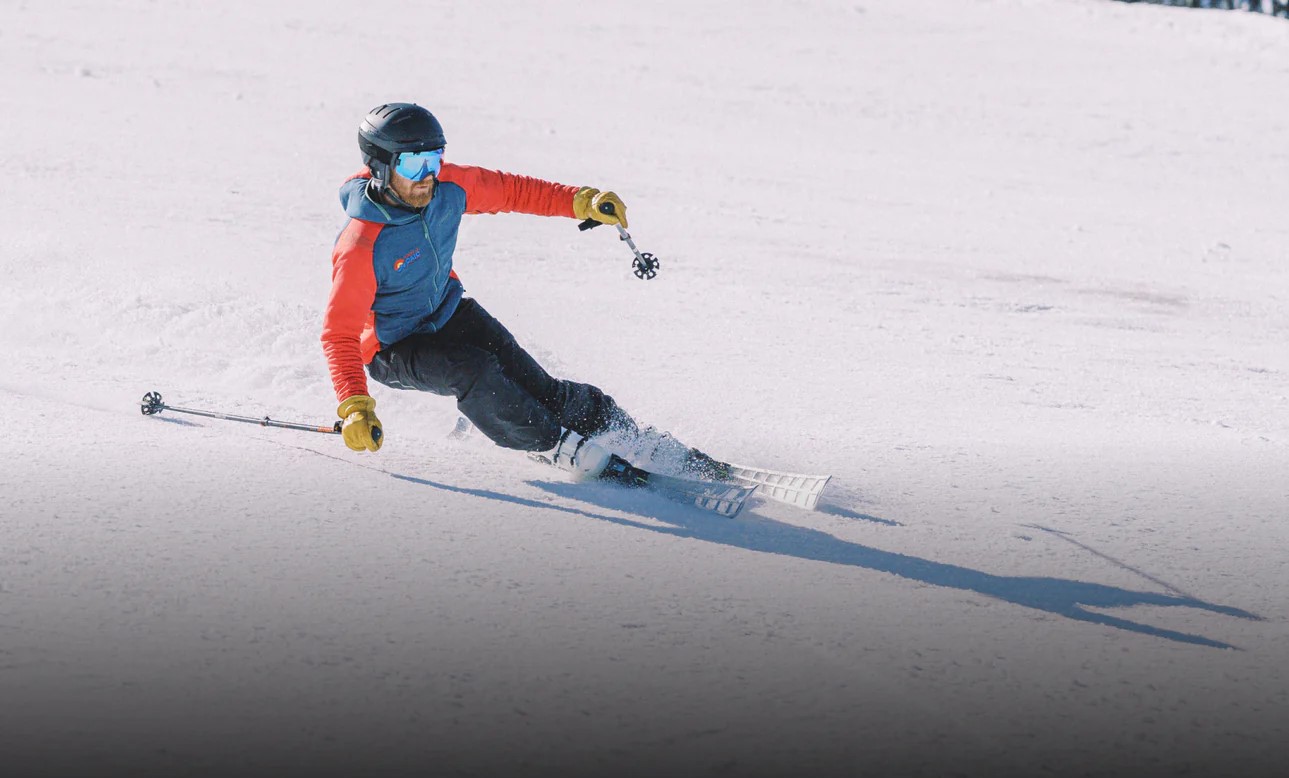
Waxing aluminum skis is a simpler process compared to traditional skis. Instead of absorbing hot wax like skis today, aluminum bases use a topical wax applied like car polish. This approach saves time and provides comparable longevity to traditional ski wax, making it practical for frequent skiers. The skis can also be tuned on todayโs ski tuning machines and because the aluminum base is so much harder than a polyethylene base, the grooving structure applied to the base by a professional ski tuning machine will last much longer. For maintenance at home, flat files and gummy stones work like they do on composite skis with steel edges.
Currently, M1 skis are equipped with a Head mounting plate and Tyrolia bindings, which can be installed by a certified dealer or service provider. However, M1 is planning to create its own mounting plate in the future, which will be a plastic component designed to be drilled for compatibility with various binding types. This design eliminates the necessity for ski shops to drill and tap directly into the aluminum.
Performance and Precision
The manufacturing process for aluminum skis offers unparalleled precision by utilizing the advanced robotics and engineering innovation of computer numerical control (CNC) machines. Using a solid block of aerospace-grade 7000-series aluminum, M1 Skis can create skis with finely tuned flex patterns and camber and rocker profiles, allowing for tiny adjustments to suit various skiing styles. With just a few hours needed to mill a pair of skis, a designer can make adjustments to a model, input the updated specifications into the CNC machine, and have the skis ready for final preparation and testing on the slopes by the next day. This precision extends to the materialโs failure behavior, because while composite skis can fail catastrophically, aluminum skis bend or crack gradually, making them safer and more reliable.
The skis are also race-ready, having received approval from the International Ski and Snowboard Federation (FIS) for use in competitive events starting in 2024. This endorsement highlights their potential to disrupt the industry at the highest levels of performance.
Eco-Friendly Innovation
Aluminum skis also stand out for their environmental benefits. Fully recyclable, they generate minimal waste during production, unlike composite skis, which often involve up to 50 materials, including multiple types of wood, metal, fiberglass, carbon fiber, plastics, and other significant non-recyclable byproducts all sandwiched together in a big, heated press. Manufacturing energy costs are easier to track, adding to their sustainability appeal.
Future Outlook
M1 Skis plans a limited release of their innovative aluminum skis in fall 2025, priced similarly to high-end alpine and race skis. While supply will initially be limited, a growing waiting list reflects the marketโs eagerness for this groundbreaking product. Reservation holders will receive exclusive access to behind-the-scenes updates throughout the production process. With its blend of durability, precision, and eco-conscious design, M1 Skis may well define the future of skiing technology. If you are an early adopter when it comes to ski gear, reserve yours today.
I thought Hexcell was the first AL ski in the 1970โs. Great ski! I still have a pair!
It looks actually really neat. The idea of a sober ski appearance, as opposed to the overpriced fashion accessory for crap pop art in increasingly garish themes, is refreshing.
As noted by several others, though, all-metal skis are nothing new. The question that is not answered in this lightly edited press release is: how does this ski dampen vibrations any better than the many metal skis before it that could not? That is one of the primary reasons that historically the best skis have always been wood core, and today almost all ski manufacturers use wood and carbon fiber construction in their top-performing skis.
Now if Metal1 was able to sell very inexpensive childrenโs skis made entirely of recycled aluminum cans at a price that undercuts the overpriced foam-and-fibreglass fashion junk that invades the slopes every year โฆ thatโs worthy of celebrating.
The other reason to focus on the juvenile market segment: you can hire Chevy Chase to apply the specially formulated no-stick aluminum cookware/ski wax to great comedic effect.
โฆ and one more thing: no adult is going to trust an aluminum ski edge. The mistaken belief that aluminum is an adequate edge material sounds fundamentally flawed. It is a recipe for daily ski edge filing, which as we all know is not what most users want. Metal1 wonโt be successful if they donโt have some compelling technology that they can demonstrate how their skis can possibly maintain a sharp & undamaged edges.
Look at the 1946 all magnesium ski. The air ski was built in Clare Michigan. They were designed by dr mconica ( who also worked on the Manhattan project) The 1948 swedish ski team used them in the Olympics. I have a pair
Thanks for reminding everyone that Howard Head was at the forefront of aluminum skis. Even if they did come apart when tested at Stowe. Great article for also capturing the Dynastar MV 2 with the Omega Rib. THAT was a FANTASTIC ski.
Sounds far fetched, as Geebee commented above. I only wish skis werent plastic! Iโll believe it when i ski it
Also see https://www.skiinghistory.org/tags/head-tey-aluminum-skis-vought-truflex-aluflex-attenhofer
First all-aluminum ski was in 1927. See https://www.skiinghistory.org/online-magazine/marie-marvingt
the ski top is going to collect a lot of snow and the ski will become much heavier
Way to shill. Aluminum edges? Yeah right. Aluminum bases holding wax? Sure. Iโd bet these will have major issues with snow freezing onto the base in any sort of variable conditions. one star.